Pharmaceutical Manufacturing Facility
Location:
Broadmeadows, Victoria
Contract:
ECI / Construction Management
Customer:
CSL Behring
Duration:
29 months
Upgrading a world-leading pharmaceutical facility in a 24/7 live environment
This project is being executed in three phases: preconstruction, early works, and main works. It covers an area of nearly 3,000 m² within an operational pharmaceutical manufacturing facility in Broadmeadows.
Key components of the project include the construction of new GMP change amenities on Level 3, the installation of specialised clean water and gas systems, a bulk process system featuring Clean-in-Place (CIP) and temperature control skids, and the addition of new fill-finish equipment, including a new aseptic filling line.
The project began with a successful Early Contractor Involvement (ECI) phase, during which Built Environs provided services such as cost planning, program development, design advice, buildability assessments, and site planning and logistics.
Due to the operational nature of the facility, several brownfield zones were carefully planned and coordinated with the client to minimize disruption to critical operations. Key activities and commissioning tasks were scheduled around four main shutdown periods, necessitating detailed programming for continuous 24/7 operations over several weeks.
Specific facility shutdown periods were identified as critical points for disruptive work, tie-ins for new installations, and modifications to existing facilities. Shutdown work included craning and rigging structural steel members, large process vessels, and fill-finish equipment through several roof and wall access openings.
The cleanroom construction involved Askin panel wall and ceiling systems, with floors finished with a durable, multi-layer epoxy coating. Building services including mechanical, fire, electrical, process waste, clean utilities, and control systems, were all installed and completed while maintaining operations in live cleanroom areas. Final tie-ins, commissioning, and validation were conducted during the designated shutdown periods.
Fast Facts:
- The project spans nearly 3,000m2 within a 24/7 operational pharmaceutical manufacturing facility
- Key works include new GMP change amenities, specialised clean water and gas systems, and a bulk process system with Clean-in-Place (CIP) and temperature control skids
- Due to the facility’s operational nature, brownfield zones were planned to minimise disruptions, with shutdown periods scheduled for key activities and commissioning tasks
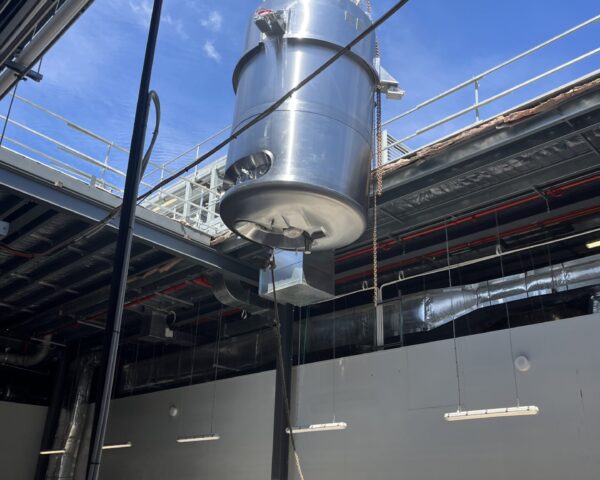
Creative Construction
Innovative rigging solutions for structural steel installation in a continuous operational environment
Construction within a 24/7 operational environment presented unique challenges, especially when installing crucial structural steel elements to form the primary platform for the new Level 3 change and gowning rooms supporting the manufacturing area. The structural platform required innovative rigging methodologies to ensure uninterrupted operations and a safe, manageable installation process. This included modifying the design of the structural steel components, such as splicing and connection details.
A specialised rigging access hatch was installed in the roof to facilitate the delivery of the main steel elements into the workspace. Once on-site, the elements were expertly manoeuvred using dollies and a manual conveyor system before being securely positioned with chain blocks.