Auckland City Hospital Central Plant and Tunnel
Location:
Auckland, New Zealand
Contract:
Construct Only
Customer:
Te Whatu Ora – Health New Zealand
Duration:
37 months
Future-proofing NZ’s largest hospital with resilient infrastructure on a constrained site
McConnell Dowell and Built Environs in partnership, are constructing a new plant building at Auckland City Hospital. This multidisciplinary project includes civil engineering, tunnelling, building and services components.
This six-storey, seismically resilient facility is the backbone of New Zealand’s largest critical services infrastructure project – designed to support hospital operations for the next 100 years. Built on a highly constrained site, it delivers essential services including emergency power, medical gases, chilled and potable water, stormwater, diesel storage, and backup systems to ensure uninterrupted life-safety services campus-wide.
Featuring industrial-grade systems, office space, lifts, and a blend of curtain wall and precast façade, the building integrates 2 x 2MVA generators, massive fuel and water storage, a treatment plant, and a 240m service tunnel linking to the main hospital. Delivered with precision and followed by a two-year facilities maintenance period, this project sets a benchmark for resilient healthcare infrastructure.
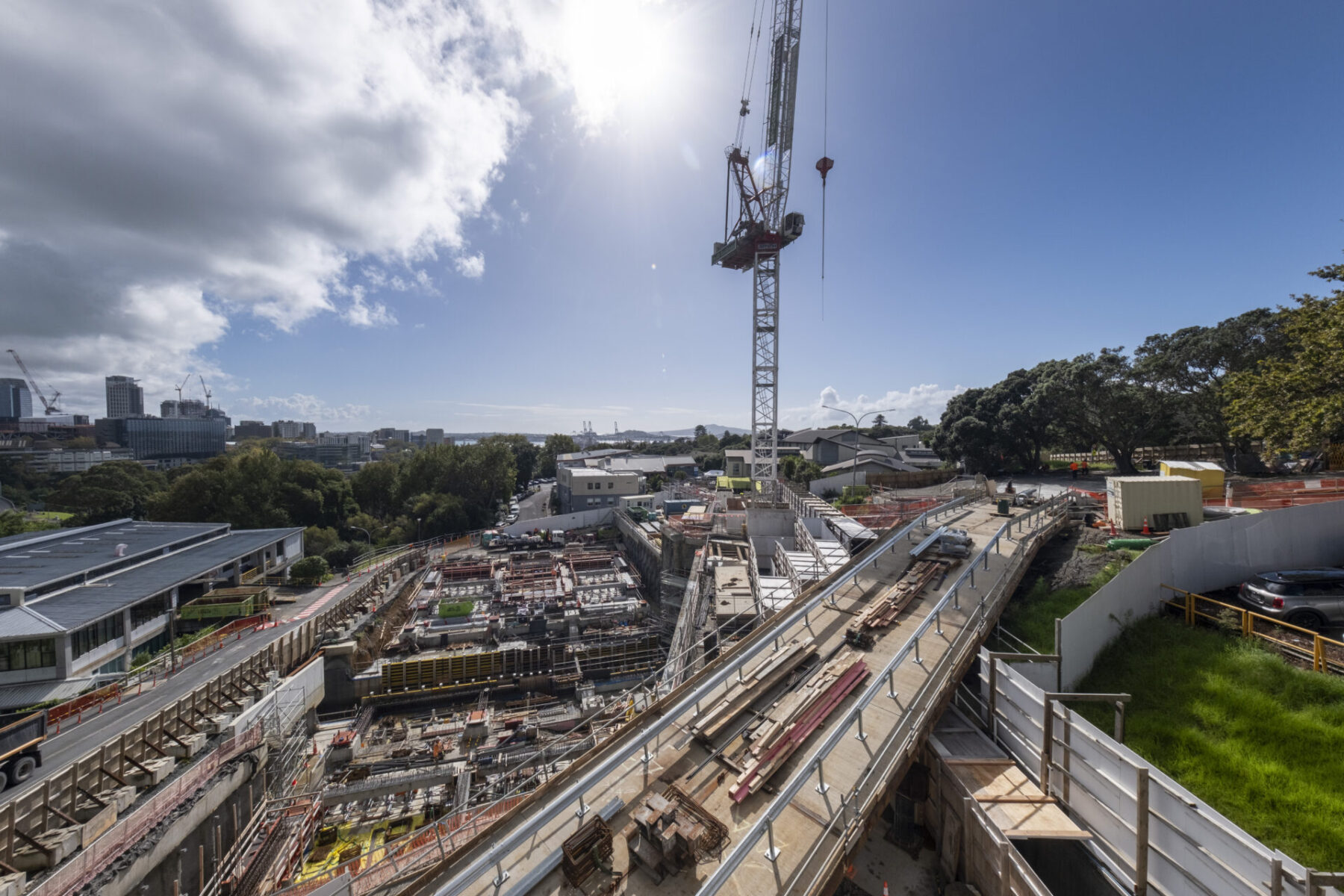
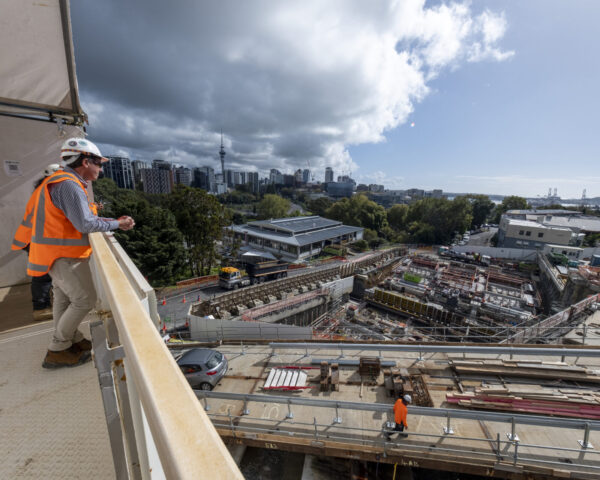
Creative Construction
Mitigating the impact of construction
At Auckland City Hospital, a complex stakeholder environment exists, with patients, staff, specialist service providers, emergency vehicles and a helicopter pad all intersecting within a limited space. To ensure the wellbeing of stakeholders, the project team have adopted the most unobtrusive construction methodology possible. Furthermore, they will be monitoring dust, noise and vibration levels through SiteHive, an innovative environmental monitor that provides real-time readings. This enables the team to respond promptly to any unfavourable construction methods that exceed the set constraints.
Achieving sustainable innovation
This project demonstrates that sustainability and innovation can go hand in hand. Our team achieved a reduction in the project’s carbon footprint of 261,248 kg/CO2-e by repurposing local materials for an inventive temporary works solution. This included 300 tonnes of steel and concrete being recycled, along with 3 tonnes of steel and 6 tonnes of concrete pads that were sourced from 18 km away from the Ngā Hāu Mangere Bridge Project, and 18 tonnes of steel from 23.9 km away at the Puhinui Plant Yard. This reuse of materials resulted in a CO2-e saving of 261,248 kg/CO2-e, and the materials only had to travel a total of 41.9 km instead of 11,160 km from China.
Fast Facts:
- A six-storey, 5,230 m2 building housing emergency services supplies to run the hospital for 3 days after a catastrophic event
- All services reticulated through a 250m tunnel to existing hospital buildings, with future expansion provision
- Replaces and upgrades services supplied from existing plant buildings and plant rooms in clinical buildings
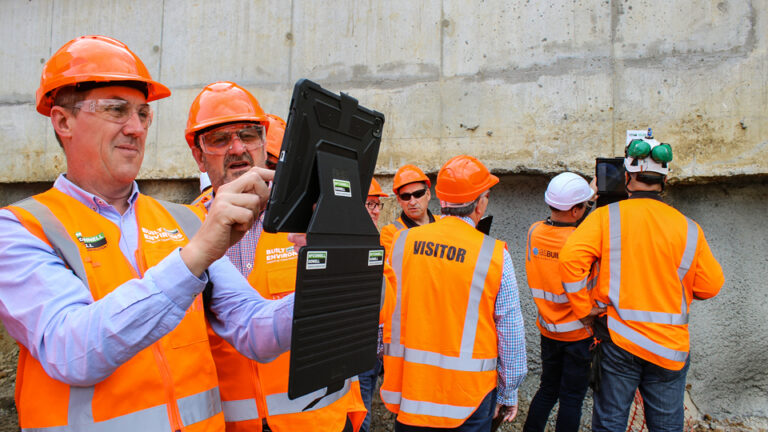