Kangkanthi Building (The Queen Elizabeth Hospital Stage 3 Redevelopment)
Location:
Woodville, South Australia
Contract:
Managing Contractor
Customer:
Department for Infrastructure and Transport / SA Health
Duration:
29 months
Increasing emergency, critical and surgical care in Adelaide’s western suburbs
The Queen Elizabeth Hospital (TQEH) has been modernised and its emergency, critical care, and surgical capabilities have been significantly enhanced with the construction of a new five-level (plus basement) clinical services building.
The building features a 46-bay emergency department, 12 operating theatres, a 14-bed intensive care unit, a 52-bed rehabilitation unit, four procedure rooms, recovery spaces, a central sterile supply department, a medical imaging department, a catheterisation laboratory, a pathology laboratory and staff support areas.
Built Environs played a crucial role from the pre-construction phase (Part A) through to construction and commissioning (Part B). Our responsibilities included:
- Conducting extensive value management
- Developing the Guaranteed Construction Sum (GCS)
- Procurement and coordination
- Testing and commissioning services for new major medical equipment, furniture, fittings, and equipment
The project was fast-tracked, with staged delivery across multiple work fronts from chassis construction through to fit-out, to ensure timely completion of this vital facility.
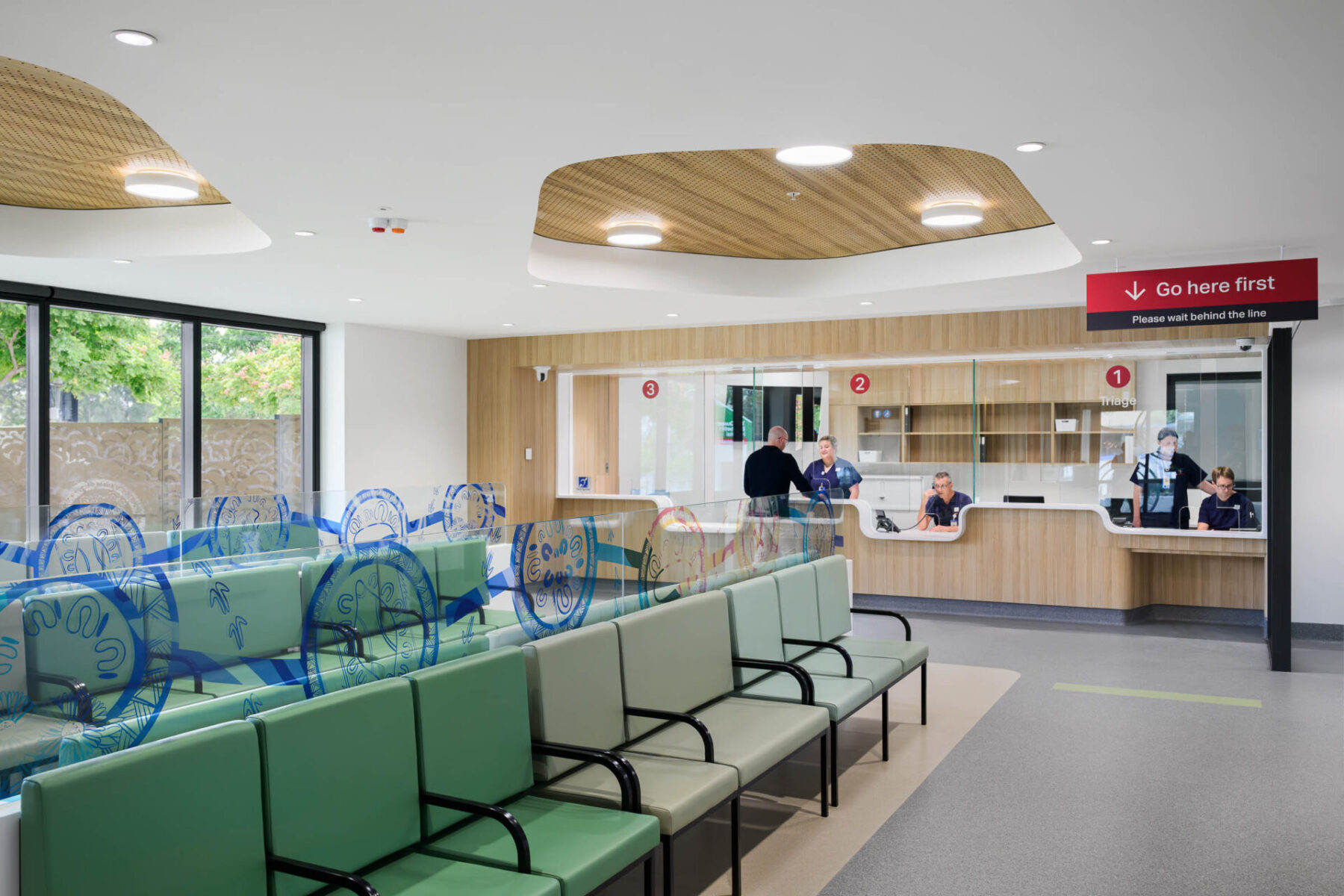
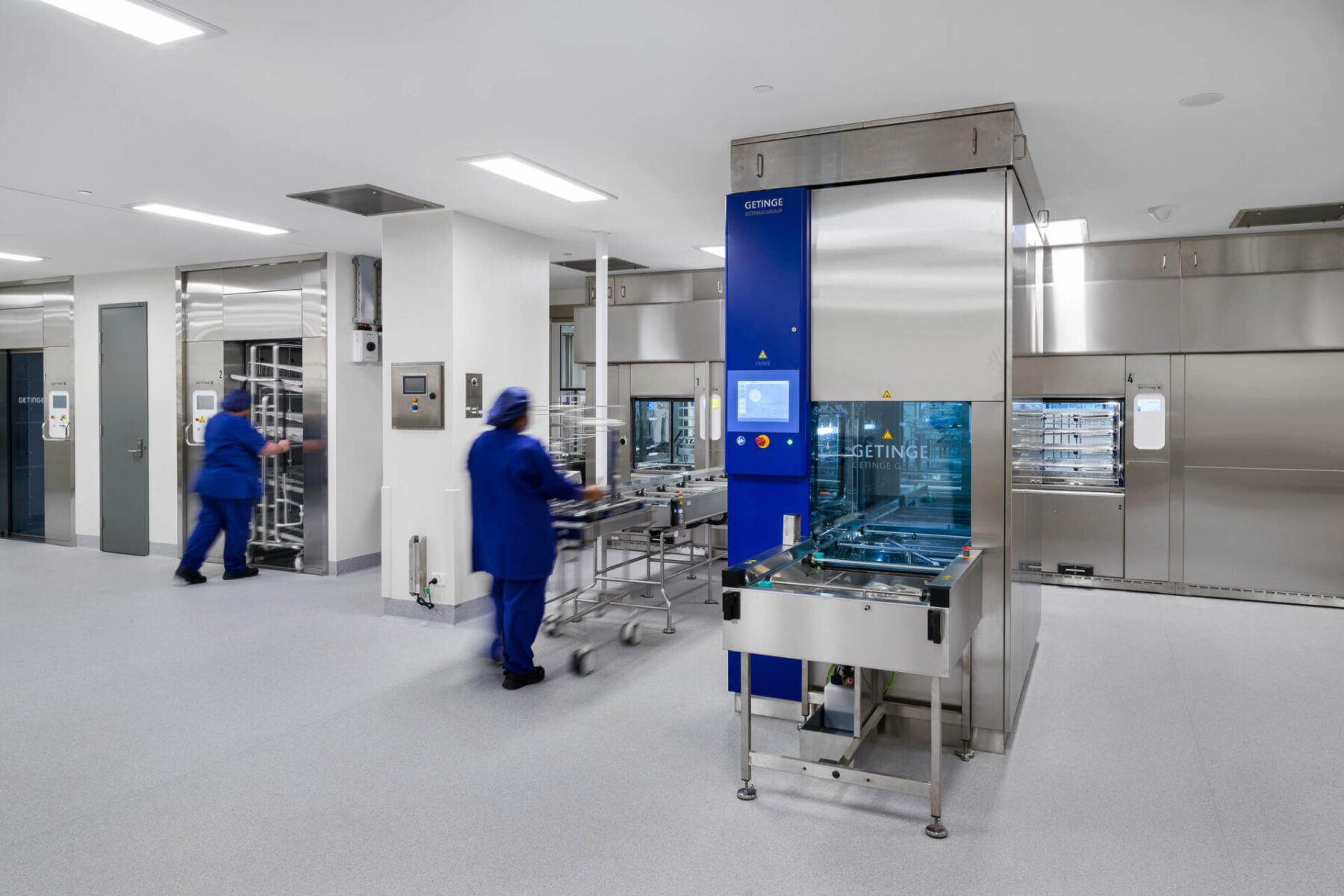
Creative Construction
With the construction site located adjacent to the existing hospital and associated health services, our delivery approach was developed to minimise disruption and keep TQEH operational throughout construction.
High productivity and reduced site congestion was achieved through our smart piling approach, while our optimised slab pour methodology provided improved quality outcomes, mitigated critical path risks and increased program certainty.
During the Part A phase, Built Environs presented a significant number of cost-saving opportunities to the client group. A substantial portion of the proposed value management savings was approved and incorporated into the project. This collaborative process played a key role in finalising the Guaranteed Construction Sum (GCS) and enabled the project to proceed under budget.
This landmark project sets a new benchmark in sustainable healthcare, with a major reduction in emissions and innovative features like tenant-controlled lifts to cut wait times. Built Environs in-house services engineers ensured clash-free installation across thousands of kilometres of building systems, delivering beyond traditional BIM coordination and driving productivity through smarter design integration.
Fast Facts:
- Australia’s first all-electric major public hospital
- 46 bay emergency department (ED)
- 14 bed Intensive Care Unit (ICU)
- 12 operating theatres including pre-operative and recovery spaces
- 4 procedure rooms and a cardiac catheterisation laboratory
- 52 inpatient beds for general rehabilitation
- SA Pathology laboratory
- 1.2m+ hours worked – no unplanned disruptions and zero complaints